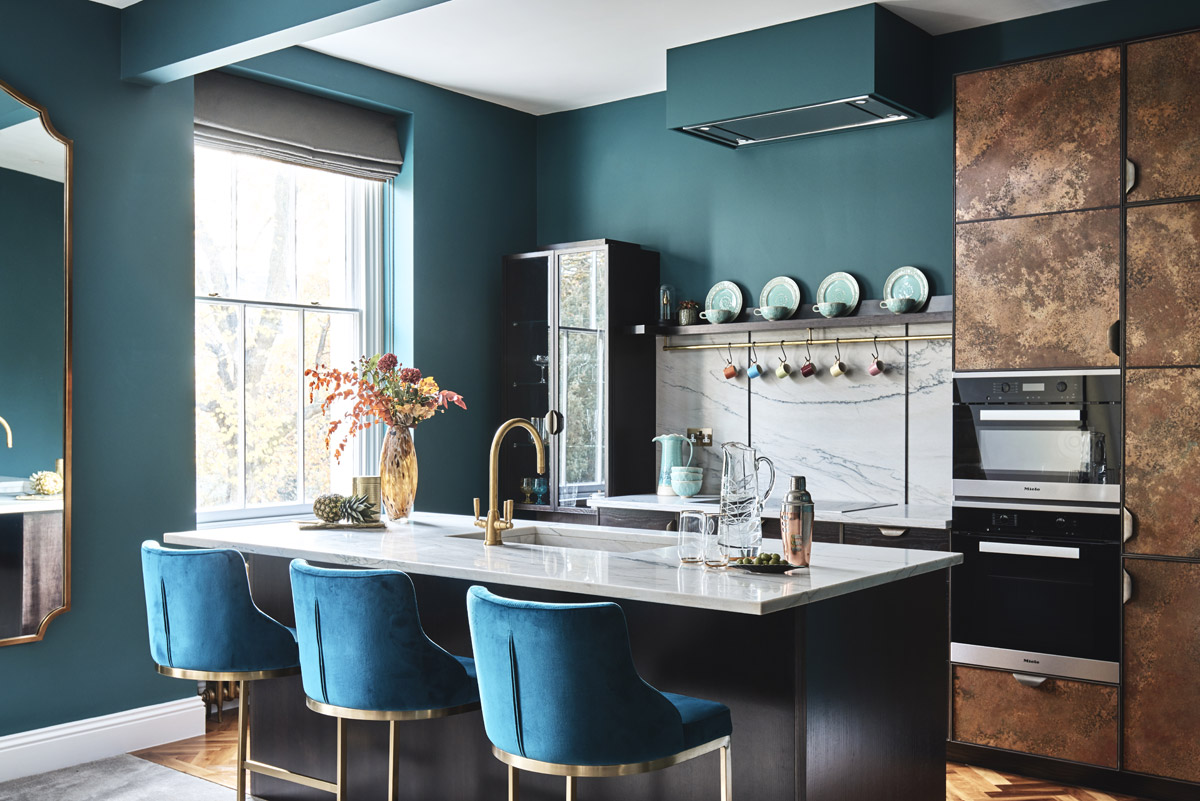
SBID Accredited Partner, Ledbury Studio opened the doors of its bespoke kitchen furniture showroom in 2019, but founder Charlie Smallbone is no newcomer to the industry. The legendary designer has been pushing the boundaries of kitchen design for over 40 years.
What is your kitchen design philosophy?
‘A kitchen is for life’. I said that to the actor George Layton in 1981, when I installed one of my first kitchen designs at his London home and I still believe it to this day. At the time, though, I think George was more concerned with the cost of the kitchen than with my musings!
That said, Ledbury Studio is much more about the future than the past – every day I look forward and try to produce something unique. I still want to deliver contemporary designs using beautiful, mostly well-known materials, but I am looking to treat them in a radical way to produce something that can’t be found anywhere else.
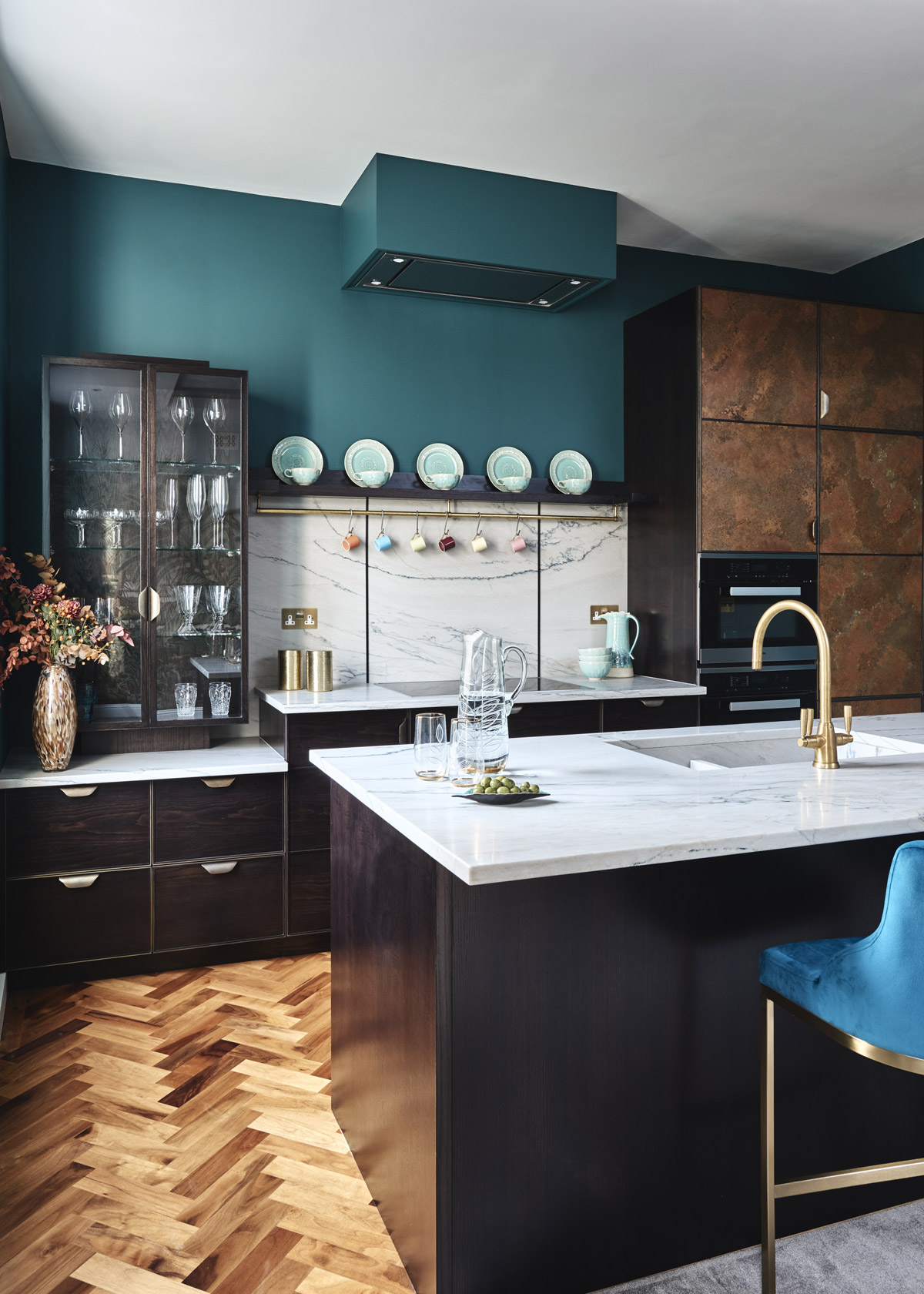
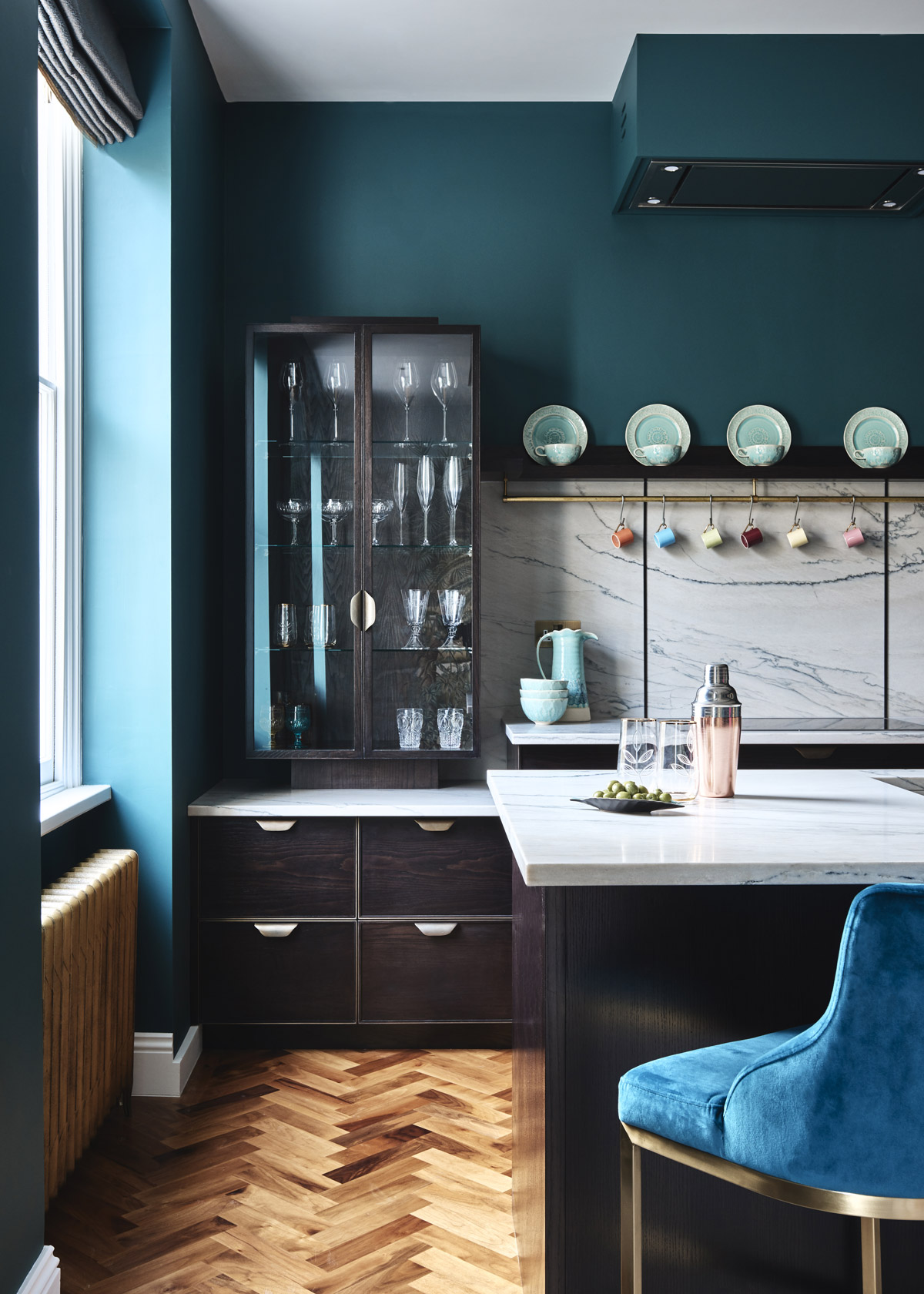
What materials did you choose to work with for your Ledbury Studio designs?
Traditionally, the use of metal in the kitchen has been largely reserved for appliances and handles, with polished stainless steel and brass the prime material choices. But having worked with both solid and liquid metal progressively for a number of years now, the idea of broadening the application of metal in the kitchen and taking it beyond its traditional uses excited me. It was also was one of my primary inspirations in founding Ledbury Studio.
From the outset I realised that this application of metals needs to be carefully executed. For this reason, I decided to take a disciplined approach with our first Ledbury Studio kitchen concept, the Metallics Collection – to use ‘metal with integrity’. So, rather than using liquid metal finishes, I opted to explore the potential of solid metals: initially copper, pewter, zinc, bronze and stainless steel. At the same time, we also considered the practicality of the finish that we were applying; aware of the potentially debilitating impact of extreme heat and water penetration. We then moved on to assess suitability of finishes in different areas of the kitchen.
Design is always about more than simply making something look nice. But I have found that incorporating these metals, and researching the different finish possibilities that each has, really does bring a unique quality to a kitchen.
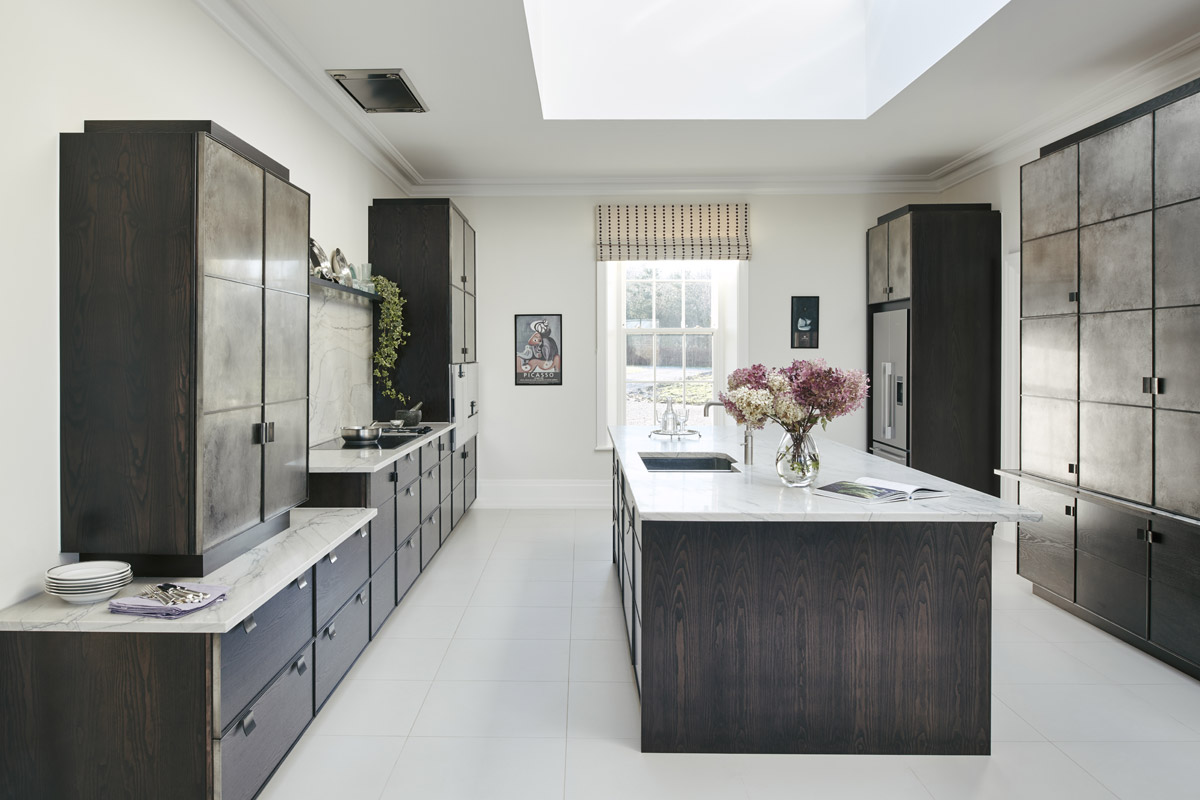
Can you talk us through the Ledbury Studio design process?
The process starts with a design consultation during which we will review any architectural plans. If clients don’t have them, we will arrange a site visit so that we can measure their proposed space and chat about how best to maximise it. At this point we are able to start putting a conceptual layout together including hand sketches and some initial 3D spatial concept modelling and material selection, based on what we have already talked about. At the same time, we will also provide an initial estimate of cost (furniture, appliances, delivery and installation).
Once we have an agreement on the basic design, budget and quote, we move forward with floor plans, 2D elevations and a formal estimate. At this point we like to create material selection mood boards and also, as required, 3D renders, as this helps us really get to grips with how the design will look and work in the space.
Finally, we drill down to specific fascia finishes, and worktop and splashback materials. By now we want our client to have a real feel for the kitchen and how individual areas of the design are going to work.
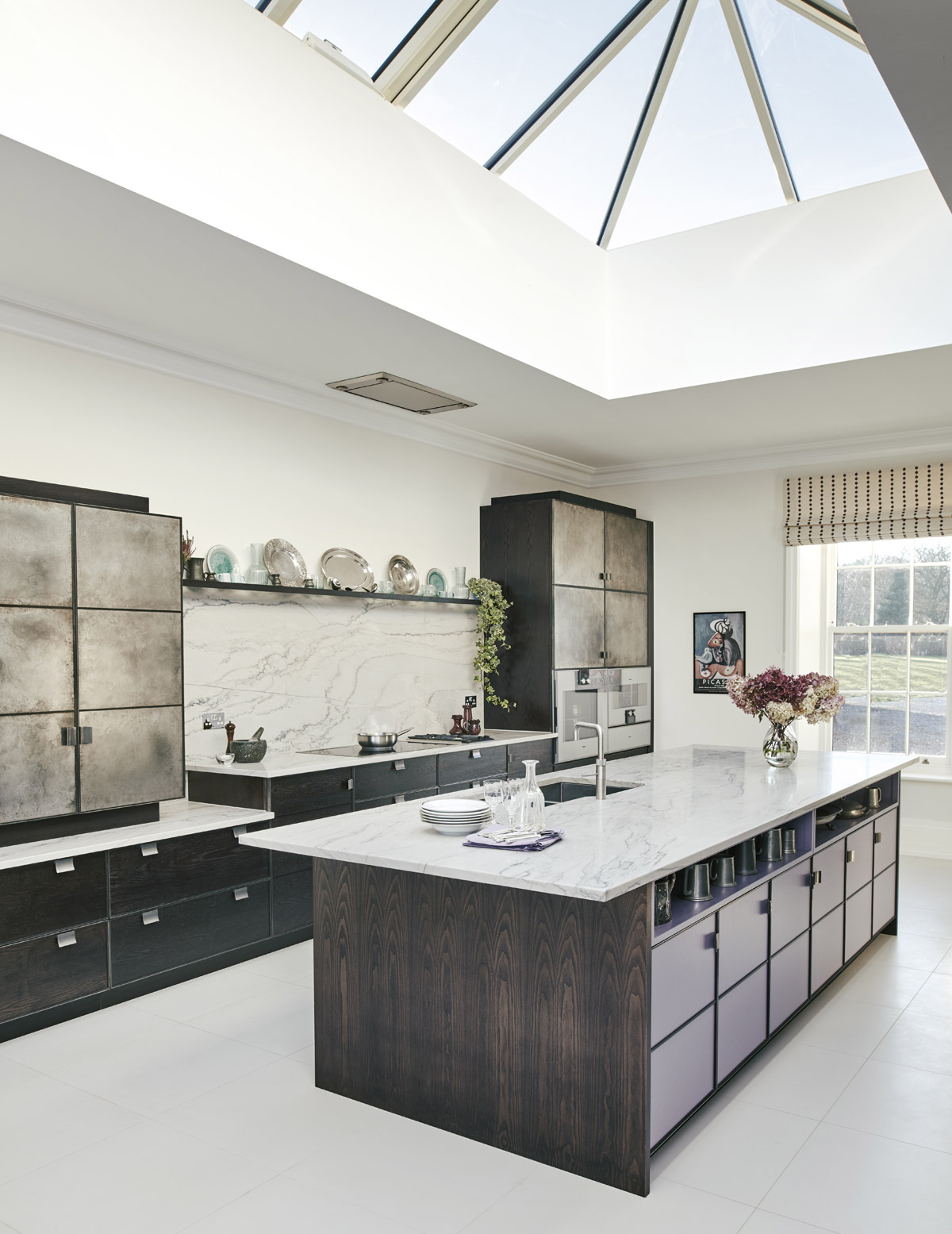
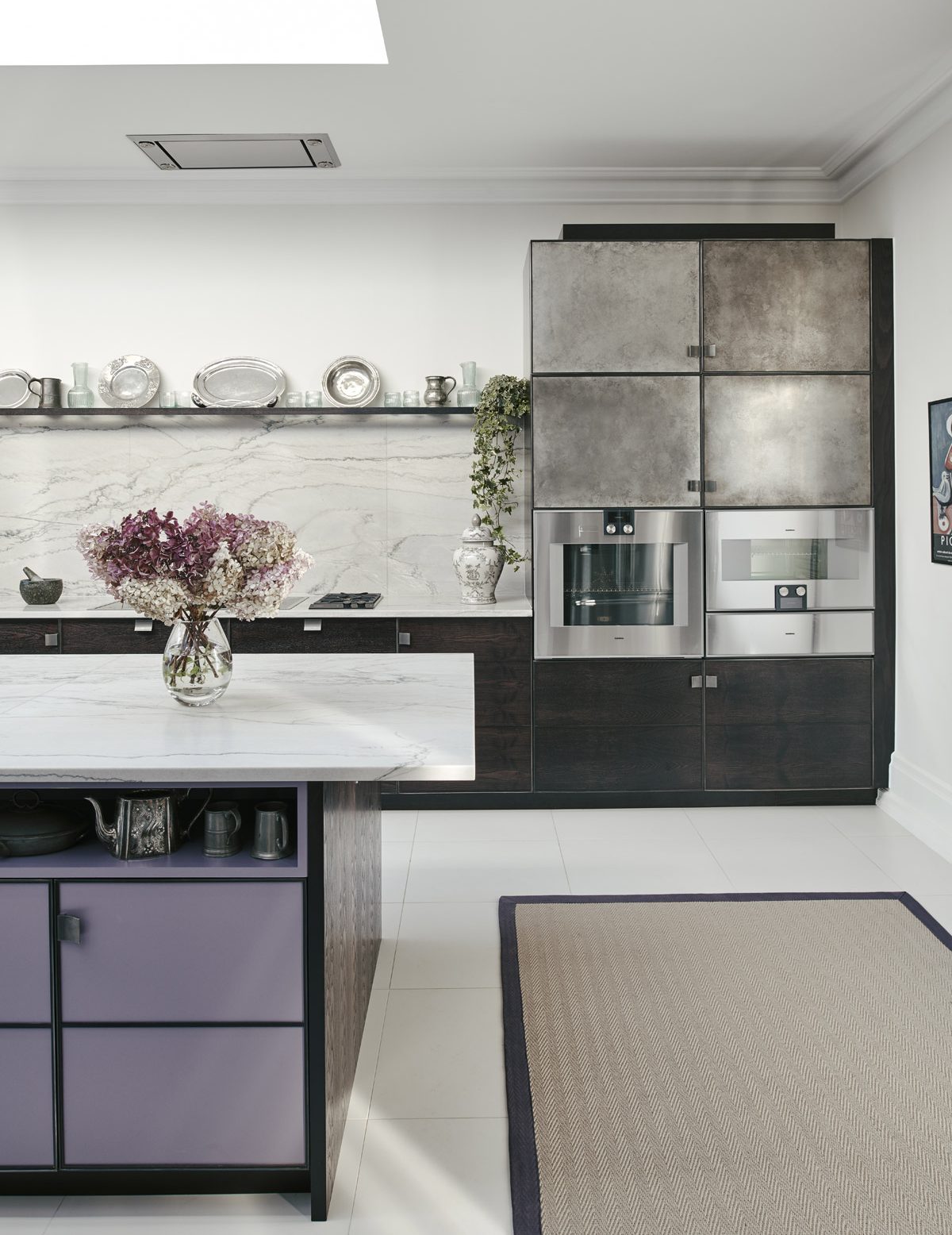
How closely do you work with you clients to create the final design?
The best kitchens evolve from a design process that is a rooted in the ideas and interests of our clients, which then combines with the design expertise of the team. This process informs initial ideas on which materials are going to work best for the kitchen design.
A good example of this was on our Cheshire Kitchen. The design was influenced and underpinned by the client’s collection of pewter-ware, which had been collected over many years. Inspired by the material, we decided to incorporate quite a number of pewter doors on the kitchen cabinetry. We ‘hand-textured’ sheets of pewter, and applied a patina using acids to age it, finally sealing the surface with lacquer.
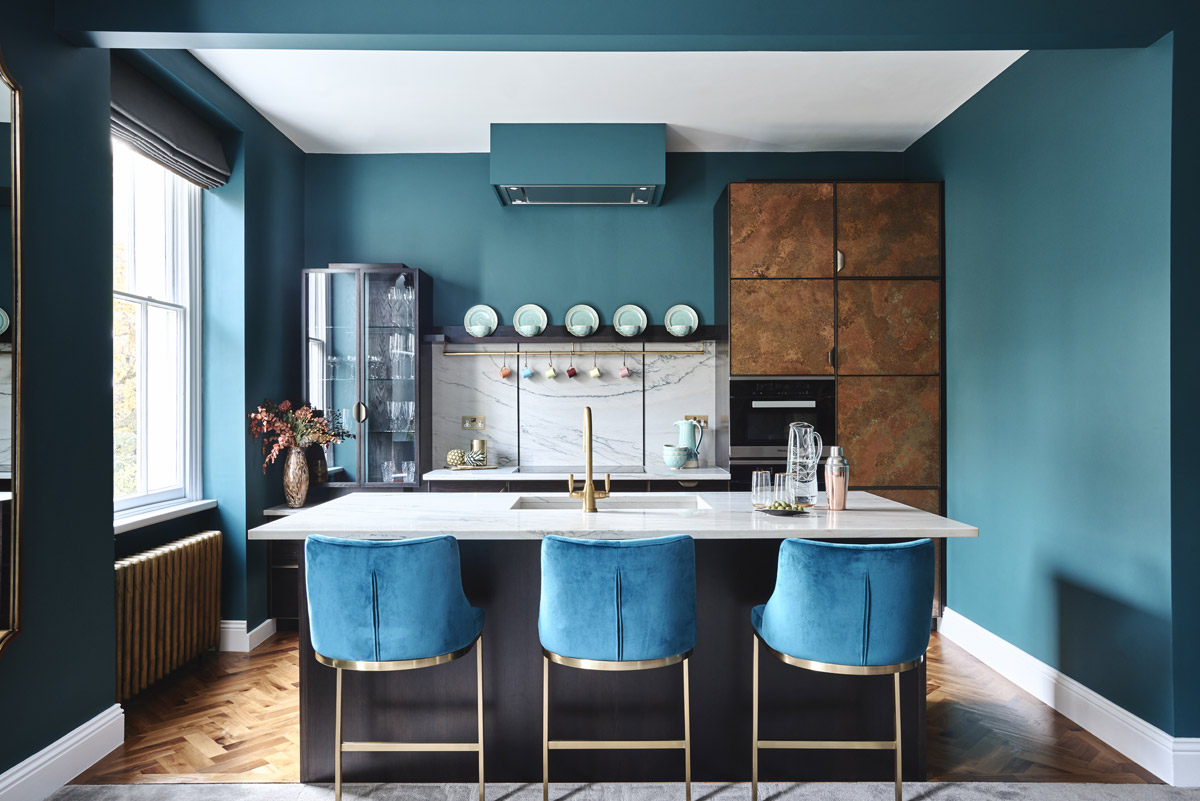
Where are your kitchens made and who do you work with?
Our kitchens are built in our Wiltshire workshop by a small team, who have worked with us for many years, from our Smallbone of Devizes and Mark Wilkinson days.
We also collaborate with a handful of talented artists and artisans: Emma Culshaw Bell, an artist and specialist painter who creates bespoke colours and finishes for our painted furniture, and designs and fabricates the Verre Eglomise incorporated into our kitchens; Quentin Reynolds, the craftsman behind our pewter door fronts; and George Winks who carves wood beautifully. We have worked carefully, on a project-by-project basis, to incorporate these elements into our furniture.
What’s the best part of your job?
It’s the enjoyment that comes from working with talented people, bringing designs to life and creating furniture that inevitably is more complex as a result of that teamwork. For me, an open and collaborative process is always infinitely more satisfying than working solo. Of course, the process needs structure. But it’s important to try to maintain enough freedom to be flexible. That way, if something unexpected and good arises, we can work to incorporate it in the final design. This is really what I love about my job – to watch the evolution of an idea, and then to see the finished result in someone’s home.
Want to become SBID Accredited? Click here for more information.